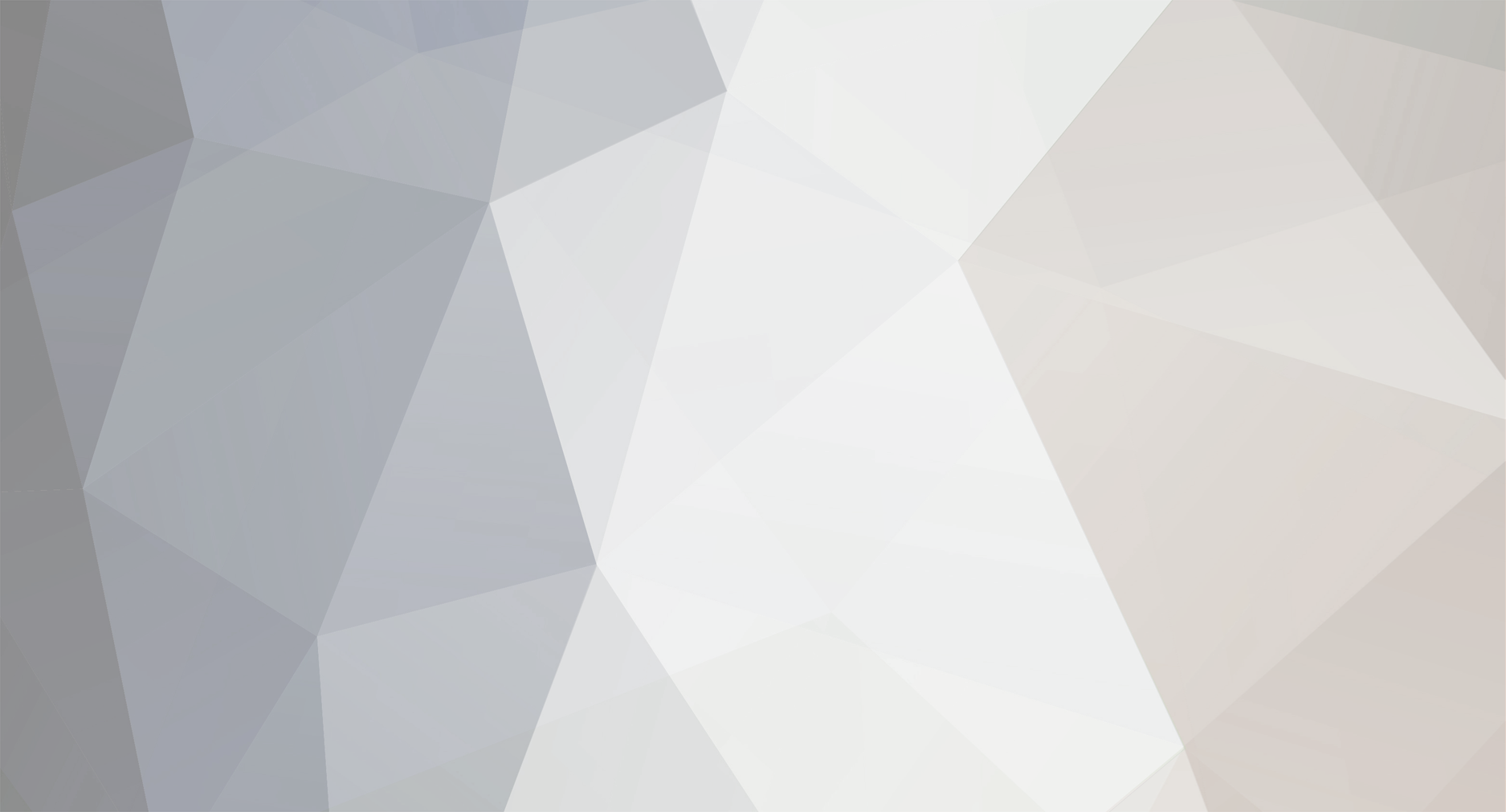
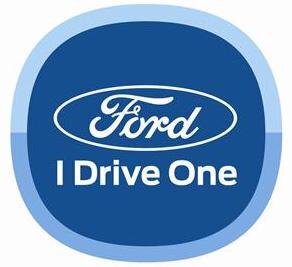
steve morris
Member-
Posts
238 -
Joined
-
Last visited
-
Days Won
3
steve morris last won the day on August 27 2011
steve morris had the most liked content!
steve morris's Achievements
56
Reputation
-
you're right, I or the union do not guarantee you your job. All we (Union Reps) can do is fight to keep work that our Union members are capable of doing in house. What you are incorrect on is when you say "contractors can always be beat if some project work is completed on straight time." The cost of UAW workers actually goes down when we have to bid work on premium time due to the fact that health insurance etc is no longer calculated into their wages at that point. The point I am trying to make having been responsible for submitting bids is that the UAW is one of the least expensive trades options out there. I have seen a hell of a lot if bids for project work from outside contractors and you would be amazed at the amount of money these guys ask for. Yet Ford is willing to pay more simply because (I hear this alot) they are not in the construction buisness, they are in the production buisness. Yet they have Highly Skilled tradesmen that are capable of doing this work while saving them money. At the Van Dyke plant, our Skilled Tradesmen have saved Ford alot of time and money time and time again. But with every new job that needs to be done, we STILL have to fight to keep the work in house. All i'm trying to say is that without a union fighting for work, this company would be more than happy to outsource the very work you and I do brother, eliminating any chance of advancement beyond production coordinator.
-
Really? You're a Union Skilled Tradesman and say/ask stuff like this? As a Skilled Trades Committeeman, My Plant Committeeperson and I fight everday to keep outside contractors out of the plant. We fight a constant battle to keep the company from outsourcing work that our people (skilled and production) do everyday. You think the company gives us this work (which keeps people like you employed by the way) out of the kindness of their hearts? As Union Reps, we have to submit bids on all kinds of work that the company would love to simply give to an outside contractor. We spend a lot of time on all of these bids and usually win them because our labor force has some of the best tradesmen and is (believe it or not) less expensive to use than most outside contactors. So before you go off asking to level the playing field for the outside contractors, maybe you should do a little homework. The majority of the time that the company wants to use outside contractors is because they don't want to manage the job or they don't have a management team with trades experience. (considering they let go most of the trades bosses and have production bosses with no trades experience supervising us) By the way, your question of "how many members think the union is doing a good job" isn't really a fair question. Just like any position, there are people that take their jobs very seriously and people that don't. Most people have a very limited view of what their Union does on a daily basis on behalf of the people they represent. There are a lot of people that take the responsibilities as a Union Rep very seriously so before you ask a slanted question like that, consider how you would like it if the same slanted question was asked about you.
-
The people on the plant floors are the only way to change things. Not all Reps are lazy and selfish but until people start paying attention and asking questions, it will be the same old same old. People on the floor have to stop putting so much stock in a what a Rep says at campaign time and start asking the people that Rep takes care of. Let his/her track record speak for itself. The other problem is that it is a thankless job and if done right, it takes a lot of time. There are some people on the floor that could be awesome Reps, but they don't want to get involved which sometimes leave us with electing the best of the worst. But until we weed out the people that aren't in there for the right reasons, things will NEVER get better.
-
The root of the problem in all aspects of this topic is GREED. Let's start with the politicians....it don't matter what party you lean towards, they're all puppets to lobbyists and big business. They sell their own country down the river in the form of faulty trade agreements all in the name of fat campaign contributions. You can't even get a bill that makes common sense passed because some idiot politicians won't vote in favor of it unless they get some bullshit added on. (which was asked for by a major campaign donor) Until ALL FORMS of lobbying are outlawed, this country will never have politicians working to improve things for us OR our country ! Correct me if I am wrong, but before all these bullshit trade agreements passed, this country was huge in manufacturing. The issue of "right to work" wasn't nearly discussed as much as it is now because people were working and making a decent living. Now that we are in a global market, we have to slash wages in order to "compete" with these third world countries that the manufacturers are going to. Since the race to the bottom started, "Right to work" it's popping up all over in an attempt to Union bust. Without a Union fighting for fair wages and safe work practices, the company can make more in profits in the name of being "competitive". The problem is that big business has done a excellent job of making the "working class" believe that union members are overpaid and spoiled when in fact we are the last group that still has what working class people SHOULD have. Fair wages and benefits compared to the companies earnings! If the company can afford to pay it's employees decent wages and benefits that they can raise a family on and still turn a great profit, why shouldn't they? Answer......GREED! what people fail to understand is that without a union, these companies would pay their employees $8.00 - $10.00 per hour without benefits and the price of the cars would not fall one bit! PROOF: the price of the cars that are being produced overseas with cheap labor have not gone down one bit. The problem with our unions is the politics that come into play. We have far too many reps that cater to the 10% of people that always seem to be in trouble or always have issues....all in the name of campaign contributions ( oops, I mean VOTES ) even when they know the employee is in the wrong. We have people running for these positions and getting elected for all the wrong reasons. These people keep getting re-elected because most people don't pay attention to how they do their job and then come election time, these Reps tell you everything you want to hear. Just like true politicians! They move up the chain and eventually get downtown NOT because of what they have done or what they know, but because of WHO they know! The majority of people that rarely need representation see all this and then see union dues being taken from their checks each month. Most of us still know the importance of having a Union but more than you think question why they should be paying dues. The Union needs to fix the way it is perceived if they want to fight the "right to work" campaign and gain more members.
-
"Ford can also form fewer and more efficient integrated teams with both production and skilled workers. The idea is to eliminate waste in the system, such as when one group must wait for another to perform certain tasks, Fleming said." This is the reason I voted No. Unfortunately, I think this was over looked by a lot of people especially in Skilled Trades. In my opinion, these "manufacturing teams" are going to cost jobs and put people in dangerous positions. Currently there are mechanical trades (PF, MW, MR, TM) in each department to cover breakdowns. In the event a a skilled tradesman needs assistance performing a task, he could ask someone within his trade that has the same knowledge and experience for help. Under the new "mechanical teams" he now is expected to get assistance from someone within his "team" which may or may not be from the same trade. This will allow the company to cut heads in Skilled Trades, Which in turn will cost production jobs considering the laid off Skilled Trades employee will go back to production. Secondly, and most importantly, This will put people at risk of getting hurt or killed. I went to college to learn MY trade, NOT EVERY TRADE. Have I learned about the other trades by working along side of them? yes. But that does not mean I can do the work of a PF or MR etc. Unfortunately, we have people that THINK they can and will be more than happy to try. We also have people out there that are to timid to tell management that they don't feel comfortable doing something. The last thing I want is for some other tradesman trying to be the hero, or to scared to say no, to do something that puts me in harms way. IT ONLY TAKES ONE MISTAKE AND SOMEONE COULD END UP BEING KILLED! I was a skilled trades committeeman when the "umbrella concept" was introduced. I heard first hand how eager management was to cut heads in the skilled trades under this program to improve their budget. If you don't think they will do the same thing under the "mechanical teams", you're fooling yourself. I was also called out on numerous occasions to prevent management from trying to force a tradesman to do something he was not comfortable doing under the "umbrella concept". This "mechanical team concept" is just going to do more of the same. The company, health and safety, you, or I cannot stop someone who is to timid to say no, or the person that wants to be the hero from doing something that shouldn't be done and putting people in harms way if we don't know what they are doing. It pisses me off that for years now the company and Union have been pushing safety (which I am all for) to the point of giving people time off for mistakes, but is so eager to turn a blind eye to the potential danger these "mechanical teams" are putting us in! Think about it, If it's not for the sole purpose of saving money, why would they be doing this? The only answer I can come up with is that safety is only important at a certain price. Could I use the signing bonus? you're damn straight I could. BUT I WILL BE MORE THAN HAPPY TO GIVE THE MONEY BACK TO SAVE MINE OR A CO-WORKERS LIFE!
-
"Ford can also form fewer and more efficient integrated teams with both production and skilled workers. The idea is to eliminate waste in the system, such as when one group must wait for another to perform certain tasks, Fleming said." This is the reason I voted No. Unfortunately, I think this was over looked by a lot of people especially in Skilled Trades. In my opinion, these "manufacturing teams" are going to cost jobs and put people in dangerous positions. Currently there are mechanical trades (PF, MW, MR, TM) in each department to cover breakdowns. In the event a a skilled tradesman needs assistance performing a task, he could ask someone within his trade that has the same knowledge and experience for help. Under the new "mechanical teams" he now is expected to get assistance from someone within his "team" which may or may not be from the same trade. This will allow the company to cut heads in Skilled Trades, Which in turn will cost production jobs considering the laid off Skilled Trades employee will go back to production. Secondly, and most importantly, This will put people at risk of getting hurt or killed. I went to college to learn MY trade, NOT EVERY TRADE. Have I learned about the other trades by working along side of them? yes. But that does not mean I can do the work of a PF or MR etc. Unfortunately, we have people that THINK they can and will be more than happy to try. We also have people out there that are to timid to tell management that they don't feel comfortable doing something. The last thing I want is for some other tradesman trying to be the hero, or to scared to say no, to do something that puts me in harms way. IT ONLY TAKES ONE MISTAKE AND SOMEONE COULD END UP BEING KILLED! I was a skilled trades committeeman when the "umbrella concept" was introduced. I heard first hand how eager management was to cut heads in the skilled trades under this program to improve their budget. If you don't think they will do the same thing under the "mechanical teams", you're fooling yourself. I was also called out on numerous occasions to prevent management from trying to force a tradesman to do something he was not comfortable doing under the "umbrella concept". This "mechanical team concept" is just going to do more of the same. The company, health and safety, you, or I cannot stop someone who is to timid to say no, or the person that wants to be the hero from doing something that shouldn't be done and putting people in harms way if we don't know what they are doing. It pisses me off that for years now the company and Union have been pushing safety (which I am all for) to the point of giving people time off for mistakes, but is so eager to turn a blind eye to the potential danger these "mechanical teams" are putting us in! Think about it, If it's not for the sole purpose of saving money, why would they be doing this? The only answer I can come up with is that safety is only important at a certain price. Could I use the signing bonus? you're damn straight I could. BUT I WILL BE MORE THAN HAPPY TO GIVE THE MONEY BACK TO SAVE MINE OR A CO-WORKERS LIFE! That's why I voted no!
-
Not sure where that smiley face came from but that's supposed to be : B)
-
Jeff, I have read a number of your posts and I just wanted to say that I respect the fact that you have the balls to speak your mind while using your real name. Also, for the most part, I agree with a lot of what you say but when it comes to this contract I have no choice but to vote it down. I'm not one of those people that expect everything we gave up to be given back right now although I do think the company should have offered a little more considering they had no problems giving back to management. I'm voting this contract down for the simple reason that we are going to lose Skilled Trades jobs and it creates a dangerous work environment. I was in office as a Skilled Trades Committeeman when they pushed the "umbrella concept" and I witnessed first hand how management tried to use that to cut heads. I also seen firsthand how management abused the language in order to try and force Skilled Trades to do work they were unfamiliar with and have seen people get hurt as a result of this. This "mechanical Team" concept will have the same results. Lets first look at job security: If I (the company) can make teams consisting of mechanical trades that is forced to rely on each other for assistance without lines of demarcation, think of the number of people I can reduce. This not only effects Skilled Trades. If Skilled trades are laid off from their trade they have the right to go back to production. Where do the low seniority production workers go when this happens? Let"s look at safety: Now I know international will tell you that if you need help from someone with your trade experience, you can request it, but in the REAL world out on that floor, I have seen the pressure that management puts on Skilled Trades in order to get the job done. DO NOT THINK FOR ONE MINUTE that they won't try and force someone to do something they are not comfortable with in order to get the line running again. If you do, you're fooling yourself ! Also, let's not forget the fact that we have Tradesmen out there that A) love to act like a super hero to management and will do anyone's job for that pat on the back B) Tradesmen that THINK they can do anyone's job and C) Tradesmen that are too scared or timid to tell their boss no when it comes to lines of demarcation and safety. Take anyone of these tradesmen and work with them under this "mechanical team" concept and you have a recipe for disaster. The last thing I want to see is me or someone I know killed or seriously injured because of something someone else does out of fear of losing his job or out of ignorance of thinking he knows it all. And with this "mechanical Team" concept, it opens the door for just that!!!! There is nothing you, I, the company, or health and safety can do to prevent it! It pisses me off that the company and International preach safety (which I'm all in favor for) with one breath but have agreed to put me and other skilled Tradesmen in harms way in the next by agreeing to this bullshit. And for those of you that think the company is going to properly train people....again, don't fool yourself. I seen the so called training when PF's and Hyd's were combined. The company is going to do as little as possible when it comes to training because training costs time and money. I can't be "my brothers keeper" and Health and Safety can't prevent the potential danger if the Tradesman doesn't tell anyone what he's about to do out of fear that his job is on the line or out of ignorance. For this reason I am voting No. If one of my friends or co-workers get killed, it won't be because I was to scared to fight for whats right!
-
I have no problem being competitive with foreign automakers wages ....when our upper management starts being competitive with foreign upper managements wages. WHY IS IT THAT ONLY THE WORKERS NEED TO BE COMPETITIVE? One ford- One team MY ASS!
-
Skilled Trades Going Back To Skilled
steve morris replied to Skilled1's topic in Ford Employee Forum
Don't bet your life on that Machine Man. When the company tried to implement the "umbrella concept", management already started to reduce trades. I saw it and heard them discuss it first hand. Now with these "mechanical Teams", the same thing is going to happen. There will not be enough buyouts and in sourced jobs to protect the skilled trades. The concept is to take one of each mechanical trades (MW, PF, MR, TM) and form a team to where the team answers repair tickets. If a PF needs help, he ask another team member, NOT another PF. How many trades in each classification do they really need if they get away with this? How many Skilled Trades are going back to production and how many low seniority production people are going to lose their jobs? How many injuries do you foresee by trades doing work their unfamiliar with because they are worried about losing their jobs if they don't? This is bad news! -
I'm voting no on this contract and I'm willing to do what ever comes from that vote! I don't expect to get everything we lost back at one time, but a cap on profit sharing and mechanical skilled trades teams is BULLSHIT!
-
You might want to ask what effect the Mechanical Teams are going to have. The way I see it, this is going to cost jobs for both Skilled and Production. When the company tried to implement the "umbrella concept" I saw first hand how management cut heads in the skilled trades while saying they don't need as many now. With the mechanical teams, if you don't think they will slash heads in Skilled trades, your dreaming. Mechanical teams will consist of one of each mechanical trade and they will go out as a "team" for repair tickets. If one trade needs help, they are supposed to get help from someone in the team-- not another person in their classification. I see two downfalls to this: 1) the company will cut the number of trades they have in each classification. In turn these tardesmen will go back to production and may cost a low seniority production person their job. 2) your gonna end up with "jack of all trades" and "masters of none" which is going to get someone hurt. You know damn well someone is going to try to play the "hero" and do something he isn't trained properly for and end up hurting himself if not whoever is with him. Also, I would love to hear why Alan Mullaly thinks its fair for his wages and stock options to be based off company performance but our profit sharing is going to be capped regardless of how well the company does. If we are in fact One Team and One Ford, Why is our profit sharing capped and his compensation isn't????? Sounds like someone is talking out both sides of his mouth to me!!!
-
I SUPPORT A FUND FOR EQUAL PROFIT SHARING
steve morris replied to novoter4life's topic in Ford Employee Forum
I didn't say repair tickets are bullshit you idiot, I said I have had production people put in tickets knowing there was nothing wrong just to get a break. It don't happen very often, but it has happened. And they may not be able to walk away at your plant when the tradesman is working on the job, but they can at my plant. So your point wasn't proven, you just don't have the ability to hear what's being said without twisting it Jackass. Obviously this conversation is going no where considering you don't have the integrity to have a honest conversation so feel free to simply go back to your assembly line and jack yourself off while telling yourself how great it is to be a "real man" in "the show" lmao -
Ford Please Stop the Musical Chairs
steve morris replied to novoter4life's topic in Ford Employee Forum
So to make sure I understand you correctly, are you actually saying that all the people at Romeo who were no longer needed should just be laid off instead of getting the opportunity to go to another plant? I mean if they lost work and don't have any work for them, what are they gonna do? Don't get me wrong, I don't want to see anyone displaced but I think ford and the IUAW are doing the right thing by allowing people to go to other locations instead of forcing them to burn their sub and tap. Now I do agree that they need to find more work at these locations as soon as possible so that they can be afforded the opportunity to go back to their basic units, but in the meantime, I think allowing them to go to other locations is the right thing to do. If I am misunderstanding your point, fill me in. -
I SUPPORT A FUND FOR EQUAL PROFIT SHARING
steve morris replied to novoter4life's topic in Ford Employee Forum
WAIT!....you actually seen a line go up before? If that's the case, How in the world can I argue with your logic? Call me bullheaded but I'm gonna give it a try anyway. Under YOUR logic; I've been to the Dentist and have had a cavity filled and even had a tooth pulled, It didn't look that difficult.....Maybe I should turn in my tools and become a Dentist! Or wait, I've taken my dog to the vet and watched them clip his nails and stitch a cut before. Didn't look to difficult. Maybe I will be a vet. Actually, I'm just teasing but I do appreciate you helping me prove my point by running off at the mouth and showing how ignorant you truly are. As far as Skilled Trades costing the company millions of dollars every year by not fixing the assembly line....you have no idea how many times trades have come out to repair a line and the supervisor refuses to allow the tradesman time to repair it the correct way because the line would be down for 20-30 minutes while the repair was being made. I have actually heard them say they will take the chance on just slapping a band-aid on it to keep the line running when they were told that if it keeps running that way, they could be looking at major down time. You have no idea how many times the correct parts weren't ordered from engineering. There are many reasons why a repair isn't taken care of properly or quickly INCLUDING some tradesmen don't want to do their jobs. But as I said before, you have people like that in ALL classifications. I could very easily think like you do and say that every recall ford has is due to production not doing there jobs correctly and not paying attention but I know better. Or I could run off at the mouth and talk about how many times a bullshit ticket came in for a repair and when I got out there, the production operator just wanted a break and asked me to take a slow look at something to give him 10 minutes and I could ASSUME ALL production people do that. The point is, I know that production people have tedious jobs and the majority of them are back breaking work, but just because I have seen some lazy asses in production does not mean I am going to categorize all production as lazy. I have seen some production jobs that were easy as hell, but I'm not gonna say a monkey could do your job. Again, I know better. You on the other hand would rather bad mouth skilled trades when it's clear you don't know what your talking about. I think the only problem we have is your not man enough to admit it! Now what do ya say we end this conversation considering the topic was meant to be on profit sharing.